Standardization is critical to every industry, and those who work in machining understand its important role. From automotive to aerospace to medical and oil, machining forms an integral component of part design and production. Parts produced must be standardized or entire product and assembly lines can fall apart. The machining industry has long been supported by standardization measures for machine tools, with standards updated periodically to remain current. Not only does this prove beneficial for part production, but machinists are better able to boost their productivity, efficiency, and throughput while lowering their cost and increasing the lifecycle of their tooling needs. Standardization for energy efficiency has gained increasing traction during the past decade. This focus could very well mean an improved ability for machine shops to contribute to the effort of promoting cleaner and greener productions. Productivity and Efficiency For CNC prototyping and full production runs, efficiency is key in providing fast throughput at a low cost. With tool standardization, both are achieved along with an improvement in the negative impact of excess tooling inventory. Obsolete tooling is responsible for a surprising amount of storage. When old tools are reintroduced over their newer replacements simply because they are kept around, efficiency and productivity levels decrease dramatically. On the other hand, when a machine shop is kept up to date with standard and improved tooling, productivity will stay on track. Improvements will also be seen in cost per manufactured unit and decreased lead time.
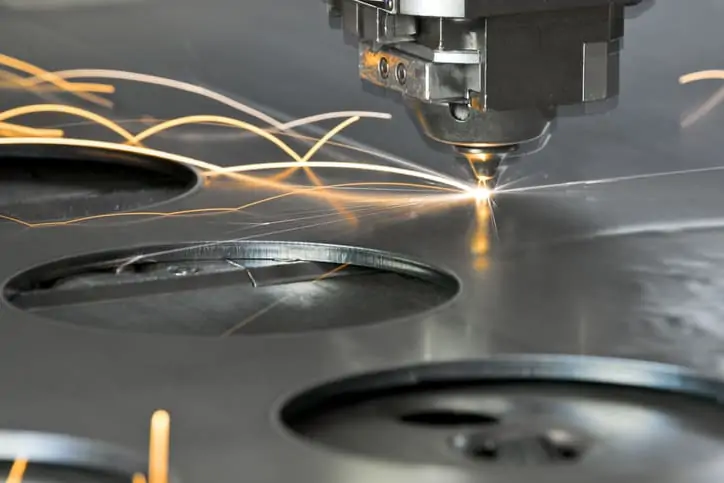
Using old tooling may be seen as a way to avoid increased tooling expenses, but this concept is faulty. While there may be higher initial output in purchasing advanced tooling, the overall expense per part will decrease. With increased efficiency, throughput will also improve. It may seem like you’re purchasing more tooling parts, but you’re actually increasing in your productivity level, which allows you to push more product through your shop and increase your bottom line.
Cost of Machine Tooling
Tooling costs easily mount into tens of thousands of dollars for machine shops, and this is often due to outdated tooling, new tooling purchased from a variety of suppliers, and small batches of unconsolidated tooling purchases. One of the biggest mistakes machine shops make is purchasing from multiple tooling shops, rather than consolidating their purchases with a few key suppliers. When tooling is standardized, machine shops can put in a larger order with a few major providers and benefit from purchasing leverage, cost reduction, excess inventory reduction, savings on floor and storage space, and a reduction in overhead costs.
Machine shop operators can benefit by going through their tooling inventory and cutting out all excess tools no longer in use and no longer up to standards. These tools have likely already been replaced and are simply wasting space. Replace obsolete or older tools with upgraded options that adhere to current standards. Consolidate your future tool purchases to include only those actively used, and purchase from one or two main suppliers to increase your purchasing power.
Energy Efficiency in Machining Standards
Every machinist knows that energy use must be factored into the total operational cost of their shop. However, until recent years, energy use wasn’t specified as its own individual ISO standard. One of the reasons for a lack of energy standardization is that machines and their operations use energy differently. This complex equation is exactly what ISO 14955-1 and ISO 14955-2 address. Some machines draw on electrical energy, others utilize compressed air, and others need hydraulic energy. There’s also sometimes unaccounted-for energy that lies within cooling and lubrication systems, in addition to other parts of the machine. For this reason, calculating and standardizing the environmental footprint of machines can be a difficult matter. However, it’s something that will be increasingly studied and focused on.
These issues are addressed by ISO standards, such as those above, that focus on standardizing the energy efficiency of machines and measuring the total energy use over the lifetime of a machine. While this is only recently in the works—within the past few years—there is no reason to think that this focus will diminish for the machining industry. As some natural resources become scarce and the global economy focuses on energy efficiency, machining and machine shops will play a significant role in reducing energy use. The more efficient machines can be, the more cost and energy savings are made possible—a goal that is right in line with the global economy’s focus on building a more energy-efficient platform for machining and total production.
Contributing Author: Christine Evans
Christine Evans is the Director of Product Marketing & Content Strategy at Fictiv, an on-demand manufacturing company. Over the past six years, Christine has grown Fictiv’s popular Hardware Guide and Digital Manufacturing Resource Center, with over 2,000 teardowns, DFM guides, and mechanical design articles to help democratize access to manufacturing and hardware design knowledge.
Article From: https://blog.ansi.org/role-of-standardization-in-machining/#gref
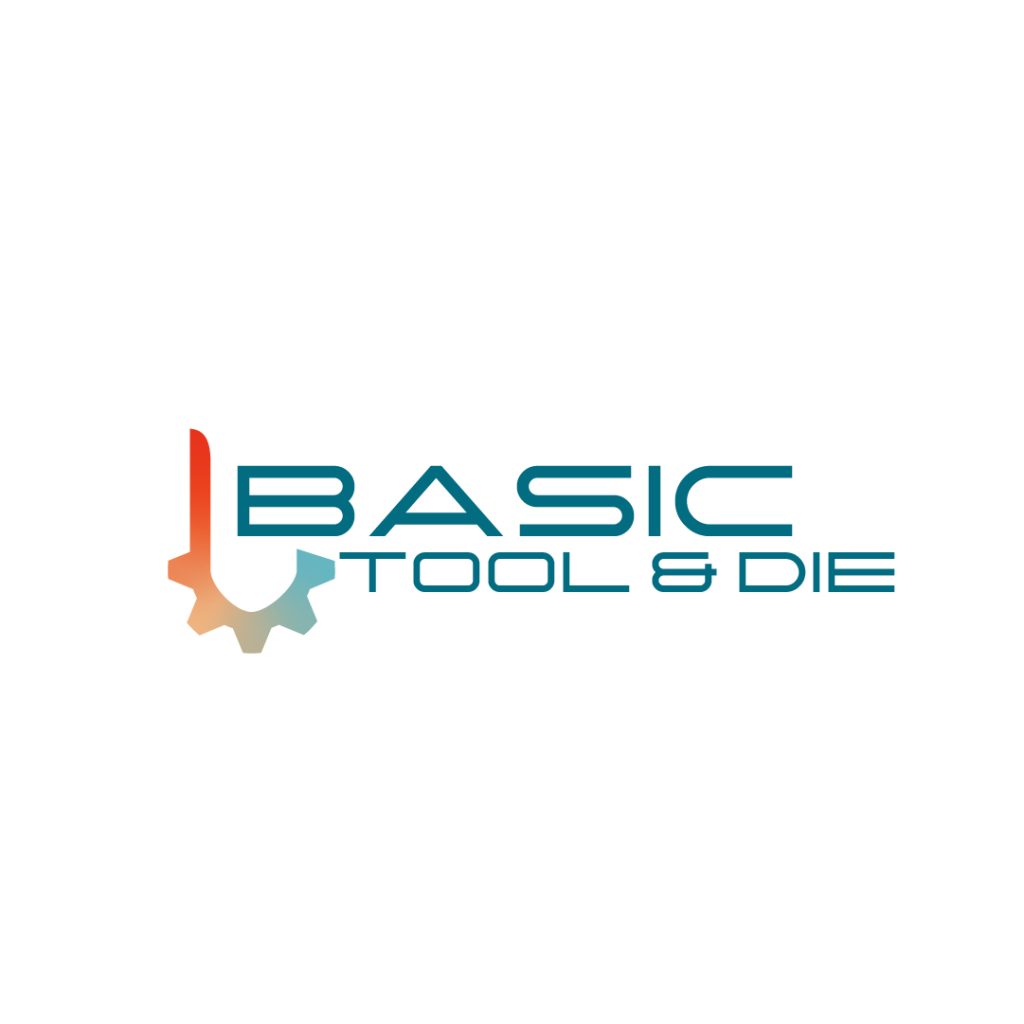