Whether you need to produce five parts or five million, finding and fixing cost drivers can be easier said than done. Often cutting costs seems like a dead certain route to also cutting quality. But that’s not the case here.
It’s time to give your production a long, hard look and truly ask yourself: Is this the best I can do to save money? Focusing on various cost factors in your manufacturing process lays the groundwork for your financial success.
And companies that are great at reducing manufacturing costs retrace these five steps over and over again.
Read our free guide and become one of them.
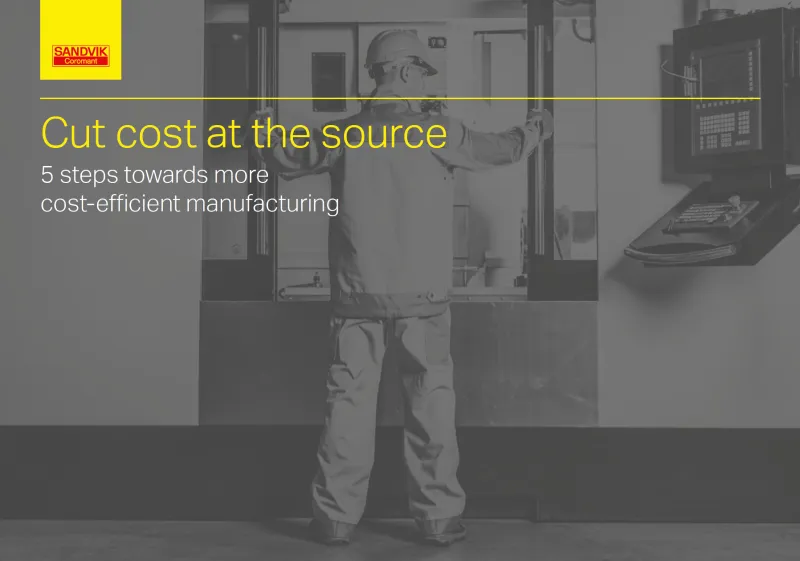
But first, get your priorities straight

In today’s competitive manufacturing landscape, reducing manufacturing costs is essential for success. A variety of cost reduction strategies can be employed to optimise the manufacturing process, minimise expenses, and boost efficiency across the production line. By focusing on reducing costs associated with direct labor, overhead, materials, energy, and maintenance, you can significantly lower your overall production costs.
When it comes to planning your machining endeavours, the size and type of production you deal with does matter as your fixed and variable costs may differ.
- Mass production? Precaution first. Losing sight of your tool inventory and other production resources could potentially detonate your entire machining process.
- Complex components? Every mistake is expensive. Plan and pre-plan, optimise, simulate, verify, and never miss out on the latest tools and solutions on the market.
- Small batch sizes? Be quick on your feet. Fast quotations, short setups, seamless flow. Process and operations planning is your sore spot.
- Mixed, recurring components? Perfectionism personified. Each process needs to be better than the last so you can make the most of it.
One effective approach to reduce costs is the implementation of lean manufacturing principles, like reducing waste, optimising processes, and enhancing quality control. Adopting a just-in-time approach to inventory management can also help minimise excess stock and supply costs, resulting in a more efficient supply chain. Using inventory software can streamline this process further, ensuring that the same raw materials are used optimally and that costs are kept in check.
Now pinpoint your pain points

In a typical workshop, this is the split between different expenses that make up the total manufacturing costs (chart on the left). Good design and planning in the early stages of a project can prevent unexpected expenditures later on. Conversely, poor machining practices and suboptimal component design can result in a significant increase in process and material costs.
This raises several important questions:
- Do you have a clear picture of your total manufacturing costs and cost drivers?
- Is your production flow transparent with access to performance data?
- Does your company have an efficient logistic solution?
- Is your company focusing on automation of manual tasks?
- Does your production ever compromise on efficiency to get stable machining processes?
Reducing direct labor costs is also an effective way to reduce manufacturing costs. By investing in employee training and using lean manufacturing principles, you can boost efficiency and productivity while minimising labor costs. Similarly, by reducing maintenance costs and implementing preventive maintenance strategies, you can save money on repairs and replacements in the long run.
Remember, data does not lie
Data is the one sole way to prove your hunch was correct all along. Digital solutions and the use of data throughout the production process boost productivity, support sustainability goals, and enable more automated machining. We like to go the extra mile in our manufacturing plant in Gimo and even gather data on things like:
- Vibration detection
- Media and energy consumption
- People competence
The best way to go about diagnosing a problem is to examine the entire value chain after all.
If you have implemented a digital solution, go back two weeks in time and look at the numbers. What do they say?
Are you in control of your tools?
Did you know that in many workshops…
Approximately 80% of work is performed with only 20% of the tooling.
30-60% of tools are not stored but piled up by the machines.
20-30% extra time is spent on administrating orders caused by delays due to lack of right tools.
To further reduce costs, you can explore cost reduction strategies such as just-in-time manufacturing or outsourcing non-core functions to specialised service providers. By focusing on their core competencies and leveraging the expertise of others, you can save money and improve your bottom line.
These are just some points to consider before you make important financial decisions. Cut down the guesswork and follow our full five-step guide to save on manufacturing costs. You might be doing some of these things already – but why not make sure? Knowing you’re doing your absolute best is the peace of mind we want to give you.
Article From:
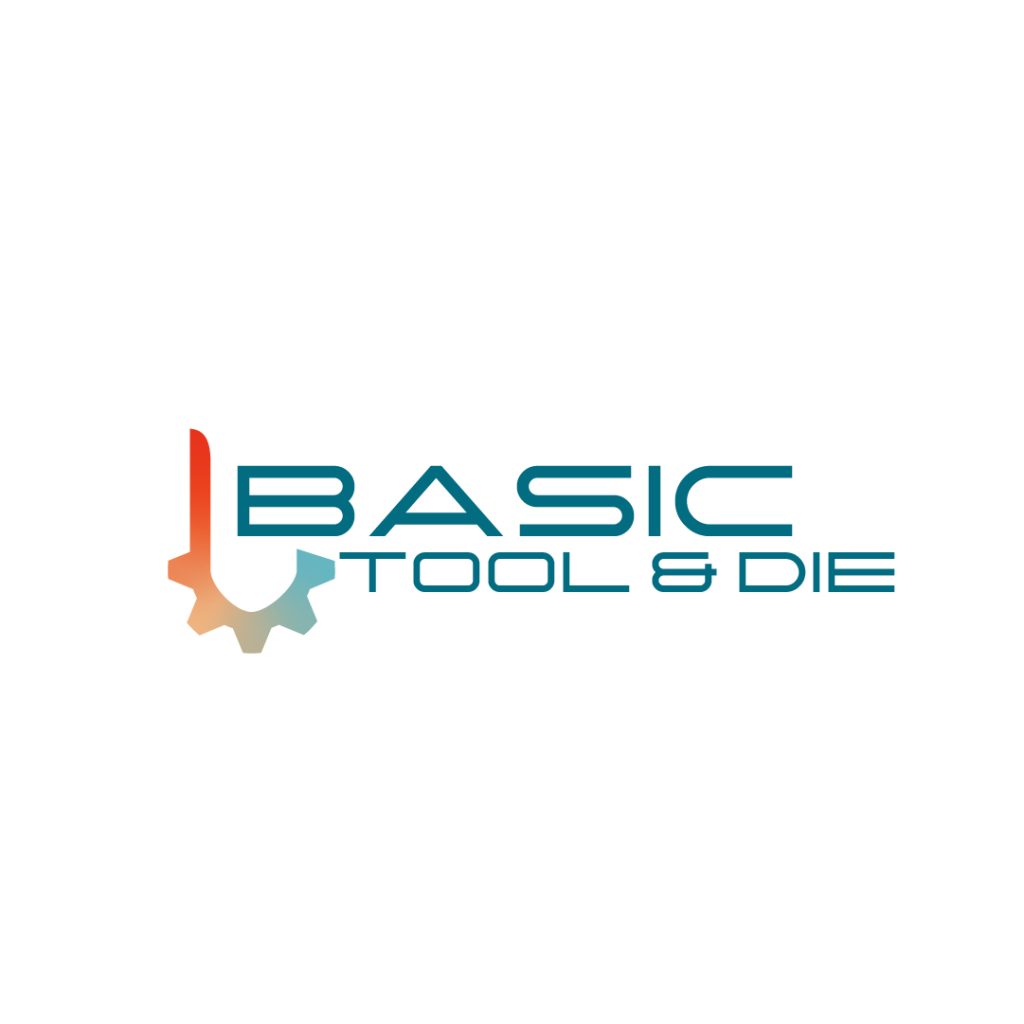