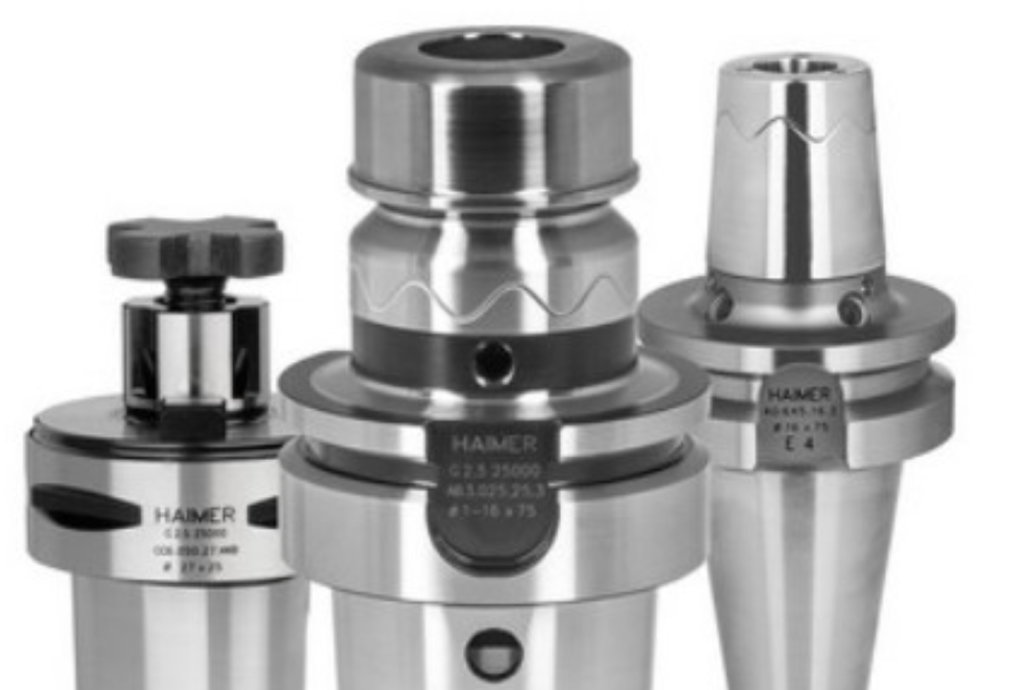
By Kip Hanson
I spoke with Brendt Holden at Haimer a few weeks ago. We discussed toolholder assembly balancing and the G2.5 standard. As the president of a company that manufactures offline presetting and balancing equipment, it’s understandable that the topic would be near and dear to his heart. According to Holden, you should feel the same way.
I’m not going into all the details of toolholder balancing here, but I will relate a story he told me several years ago. It was about a shop owner who’d bought a balancing machine from Holden after investing in his first 20,000 RPM CNC machining centre, a move that makes perfect sense for anyone who wants to improve part quality and extend tool life, not to mention that of their machine’s spindle bearings.
The interesting part was when Holden revisited the shop several months later. During a slow period, the owner had balanced every toolholder assembly in the shop, even though the rest of his machining centres were limited to 8,000 RPM. According to Holden, the man was overjoyed—not with better tool life or part surface finish as one might expect, but with productivity.
READ NEXT:
Ask the Expert: Zero-Point Workholding – Shop Metalworking Technology (shopmetaltech.com)
Ask the Expert: Machine Probing – Shop Metalworking Technology (shopmetaltech.com)
“He had all these 20-year-old Hitachi Seikis, and where before he might run 3,000 RPM on a finishing pass, he was now able to double that, with a corresponding increase in feedrate.”
Then there was a related story from the owner of a spindle repair company. When asked if he thought balancing at 8,000 RPM is a good idea, his answer was a resounding, “Absolutely.” Coming from a guy who makes a living rebuilding machine tool spindles, it seemed like quite a testimonial.
Granted, Holden and other tooling manufacturers (many of whom admit to using Haimer equipment) will tell you they pre-balance their toolholders to G2.5 at 20,000 to 25,000 RPM, depending on the company. For shops with 12,000 RPM spindles, this should be plenty good, they say, even once you’ve added a retention knob, collet nut, variable helix end mill, and other components to the toolholder assembly, all of which tend to increase imbalance.
I’m sure they’re right, but then I wonder about that shop owner who found himself with too much time on his hands and balanced everything in his shop. His story and that of the machine spindle rebuilder make sense to me, especially given that both offered that information with no prompting.
I’ll relate one final story, this one from my own experience. While standing in front of a Hardinge Handscrew at my first machine shop job in 1978, the crusty old machinist charged with training me said, “It doesn’t matter how you do it, as long as you do it the same way every time.” He was referring to gripping the machine handles, but it’s a lesson that’s stuck with me ever since.
IMHO, successful manufacturing comes down to removing as many variables as possible, and imbalance is one of them. Yes, it might be overkill in some applications, but then again, it’s worth evaluating for yourself. Every little bit helps, right? SMT

TECHNICAL EDITOR KIP HANSON has more than 40 years experience in the manufacturing industry. He is the author of Machining for Dummies and Fabricating for Dummies and has written over 1500 articles on a diverse range of metal manufacturing topics.
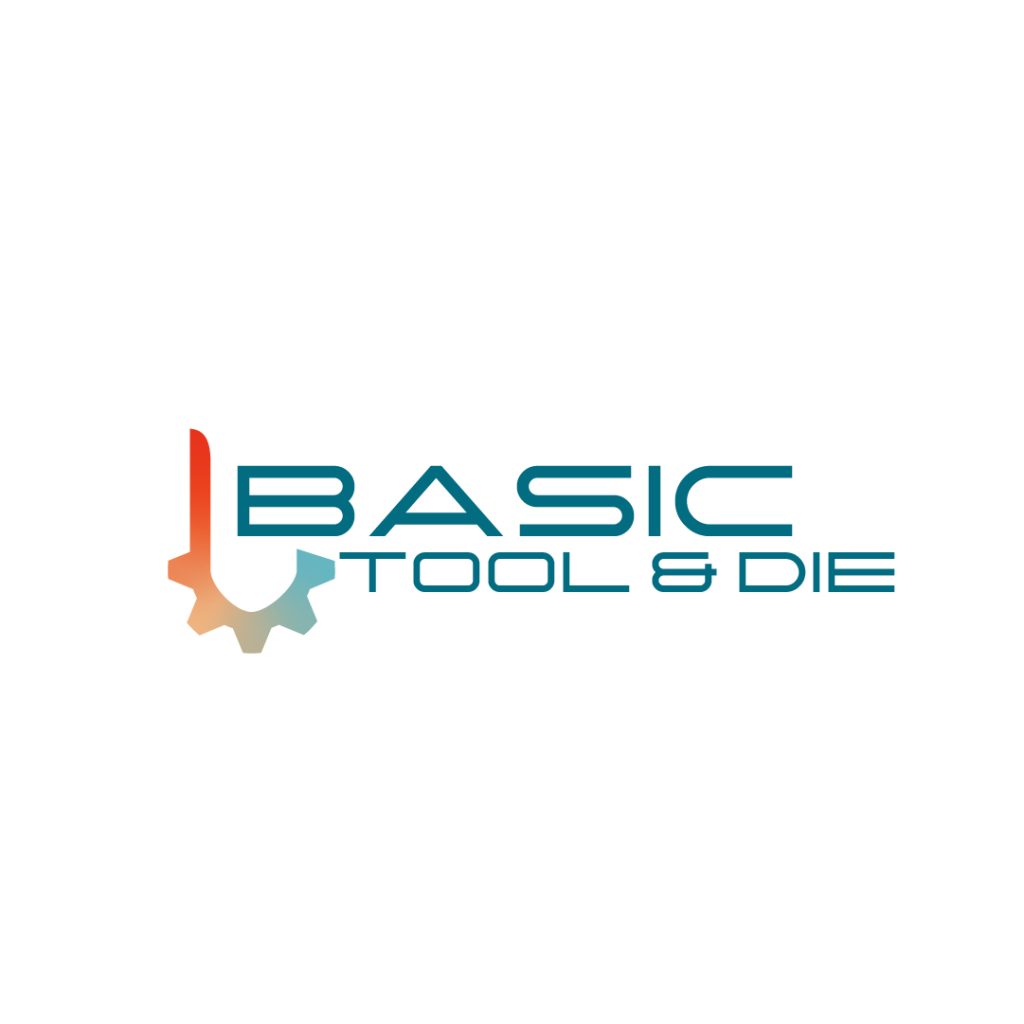